Transporeon makes moving freight as easy as possible.
For more than 20 years, Transporeon has been digitising and transforming logistics. The Transporeon transportation management platform is an essential part of the shipper/carrier ecosystem while linking people, places and things.
We connect, encourage collaboration, enable efficiency and automate ease for transportation operations and supply chain with our autonomous dealmaking, execution & visibility, dock & yard management and tech-driven freight audit solutions.
AI, data-driven analytics, autonomous, automation…these are buzzwords for some, but they are built-in for us. Transporeon’s cloud-based transportation management software enables thousands of customers every day, and powers the largest network of shippers, suppliers, retailers, goods recipients and carriers in the world. And as the newest member of the Trimble family, that network is now even bigger.
Got freight? Get Transporeon.
The company we keep
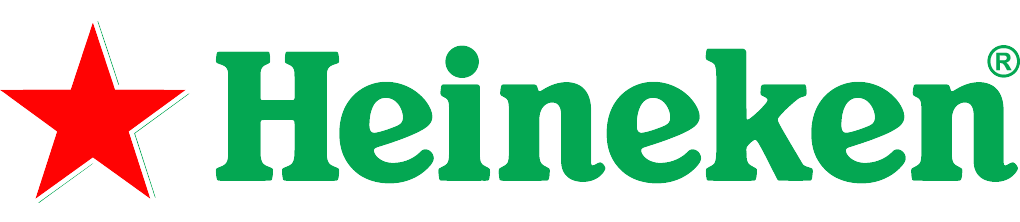
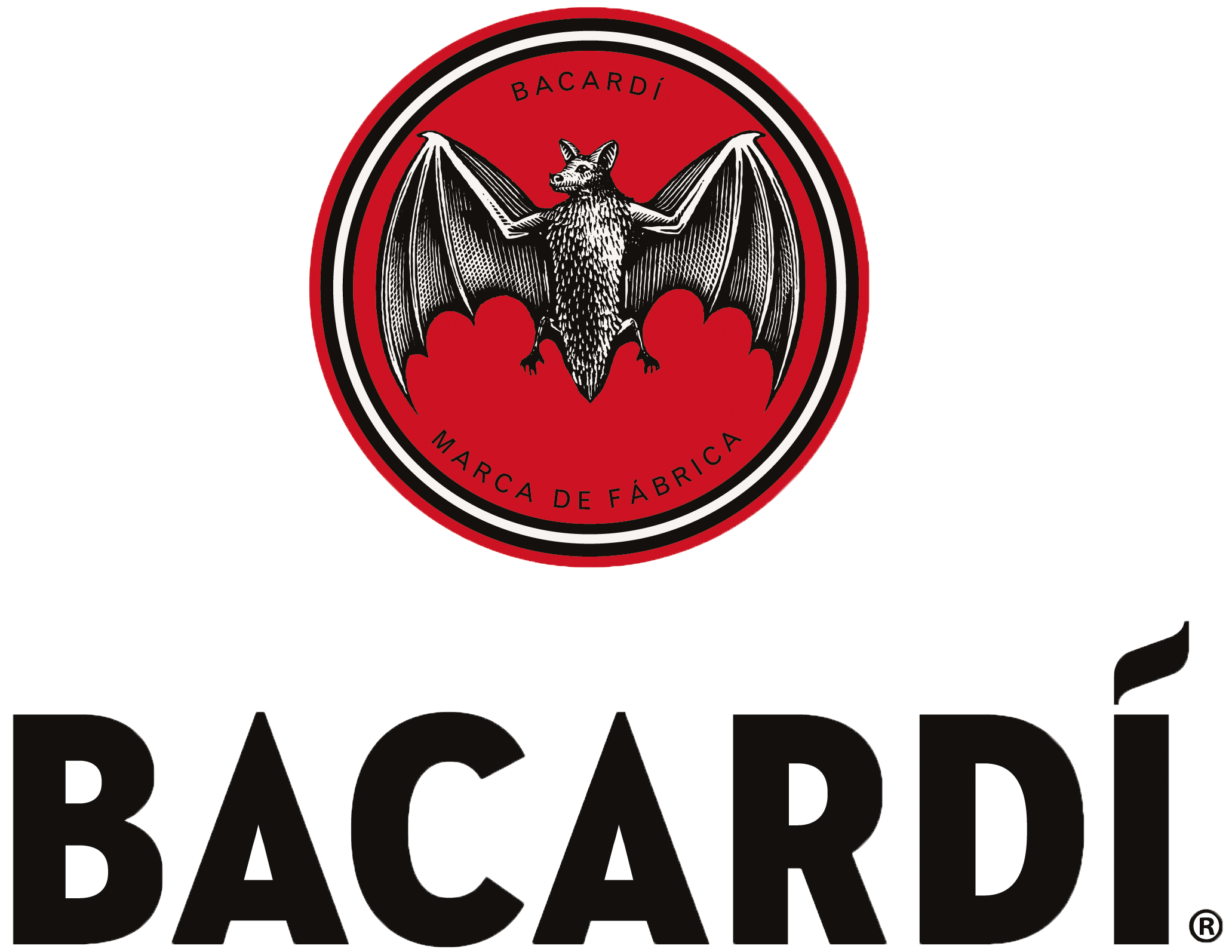
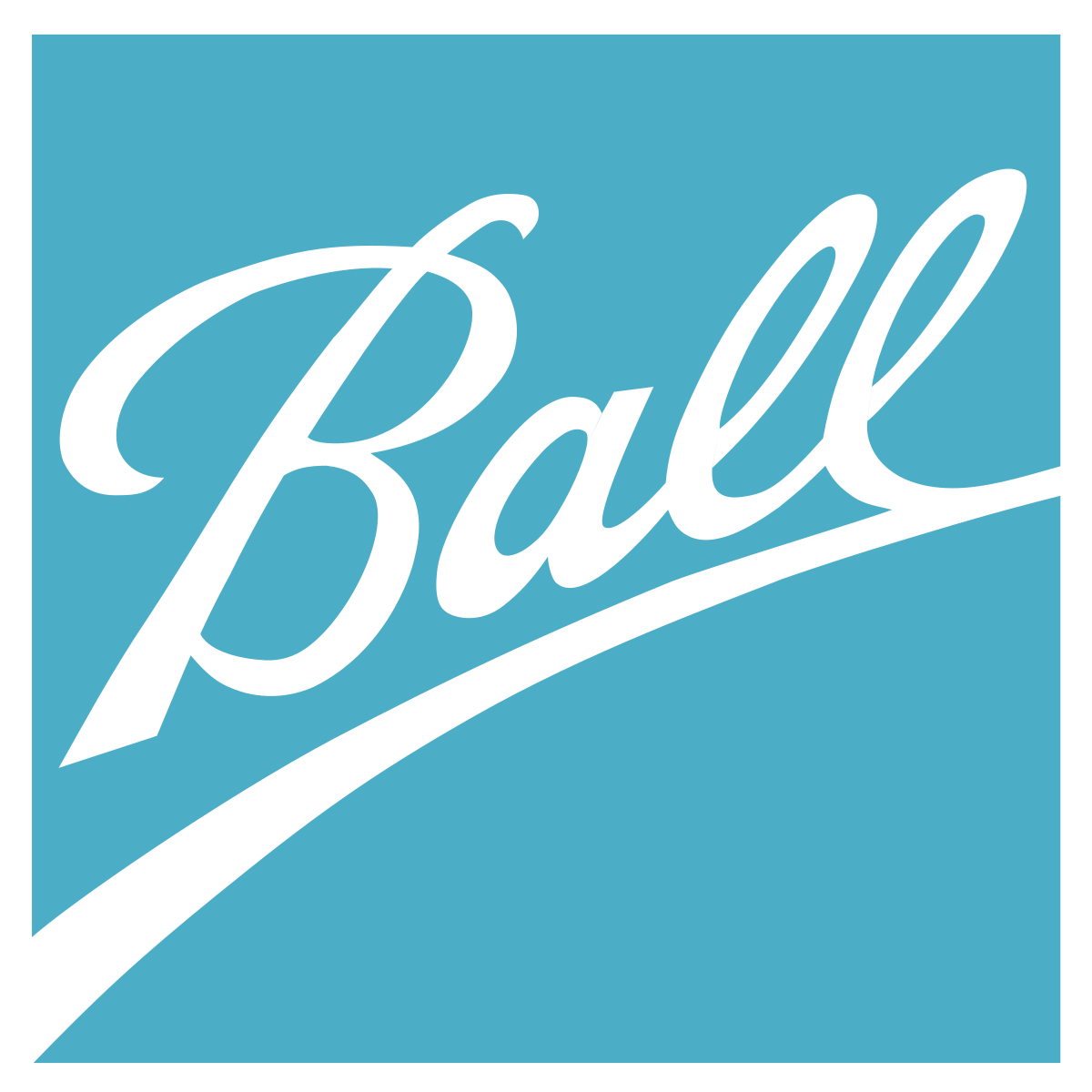
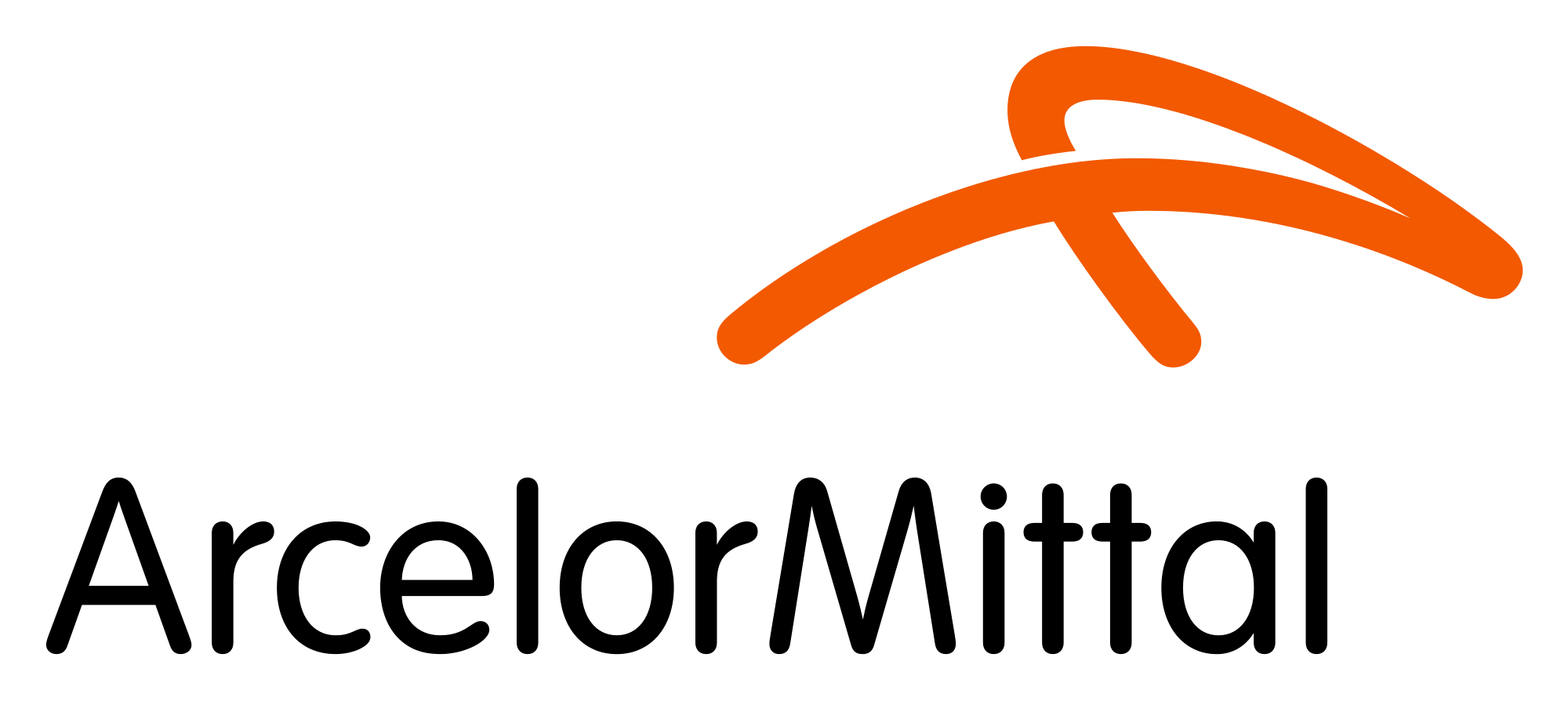
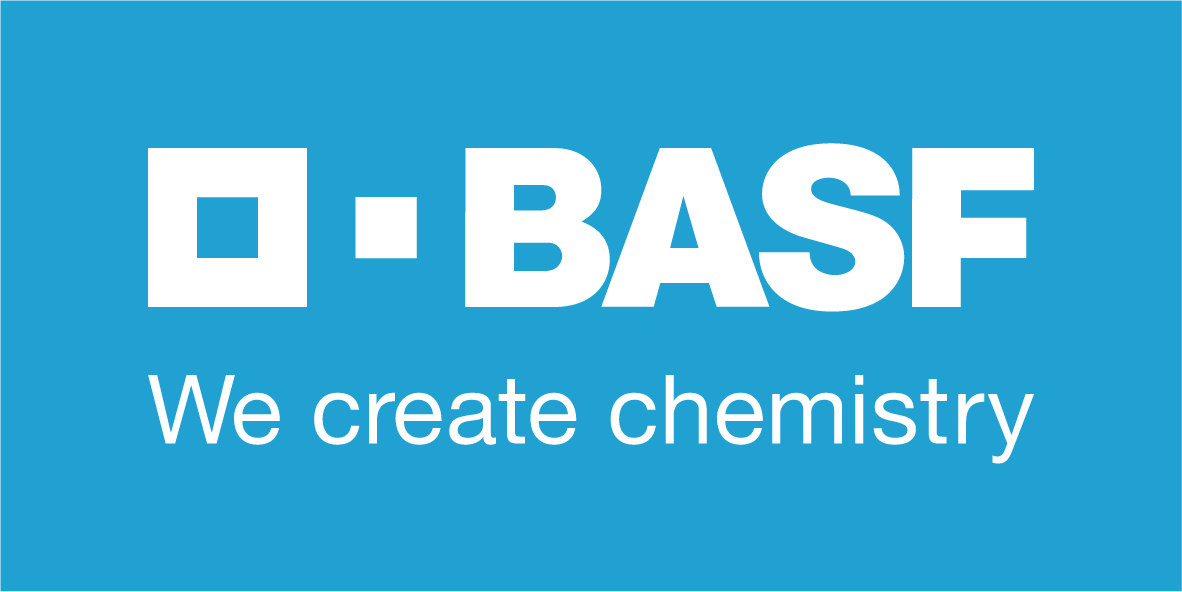
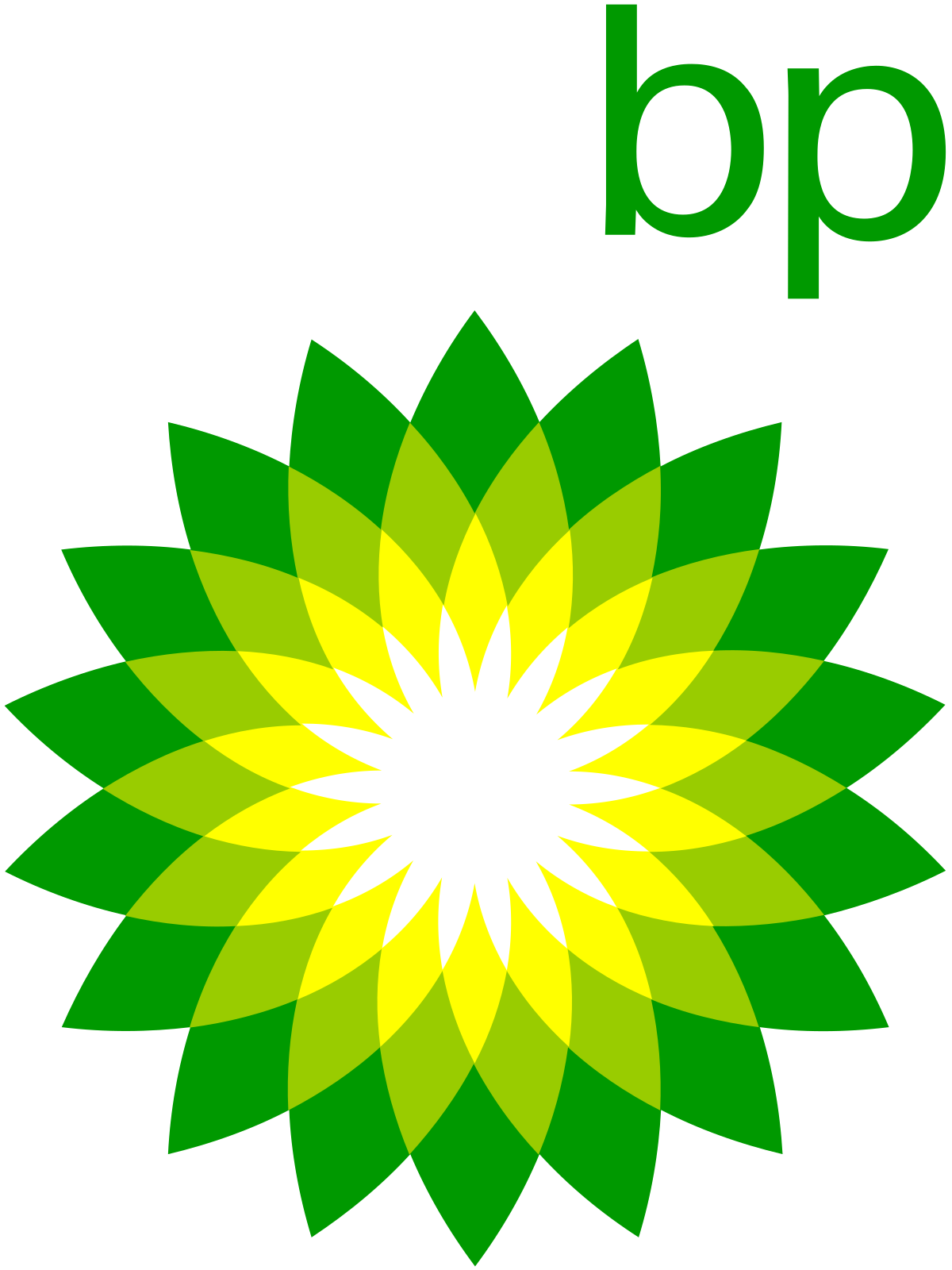
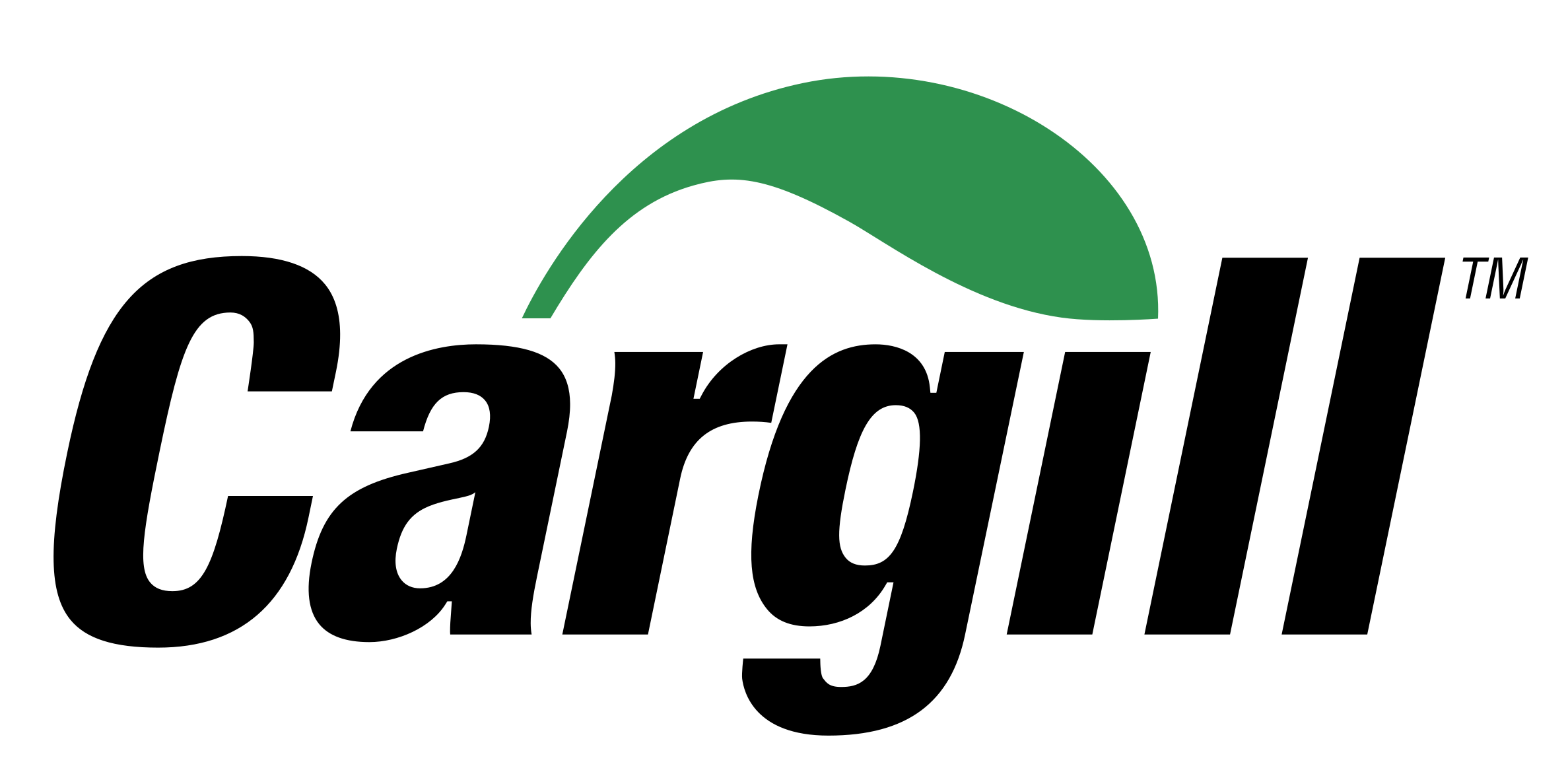
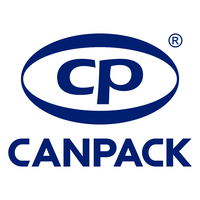
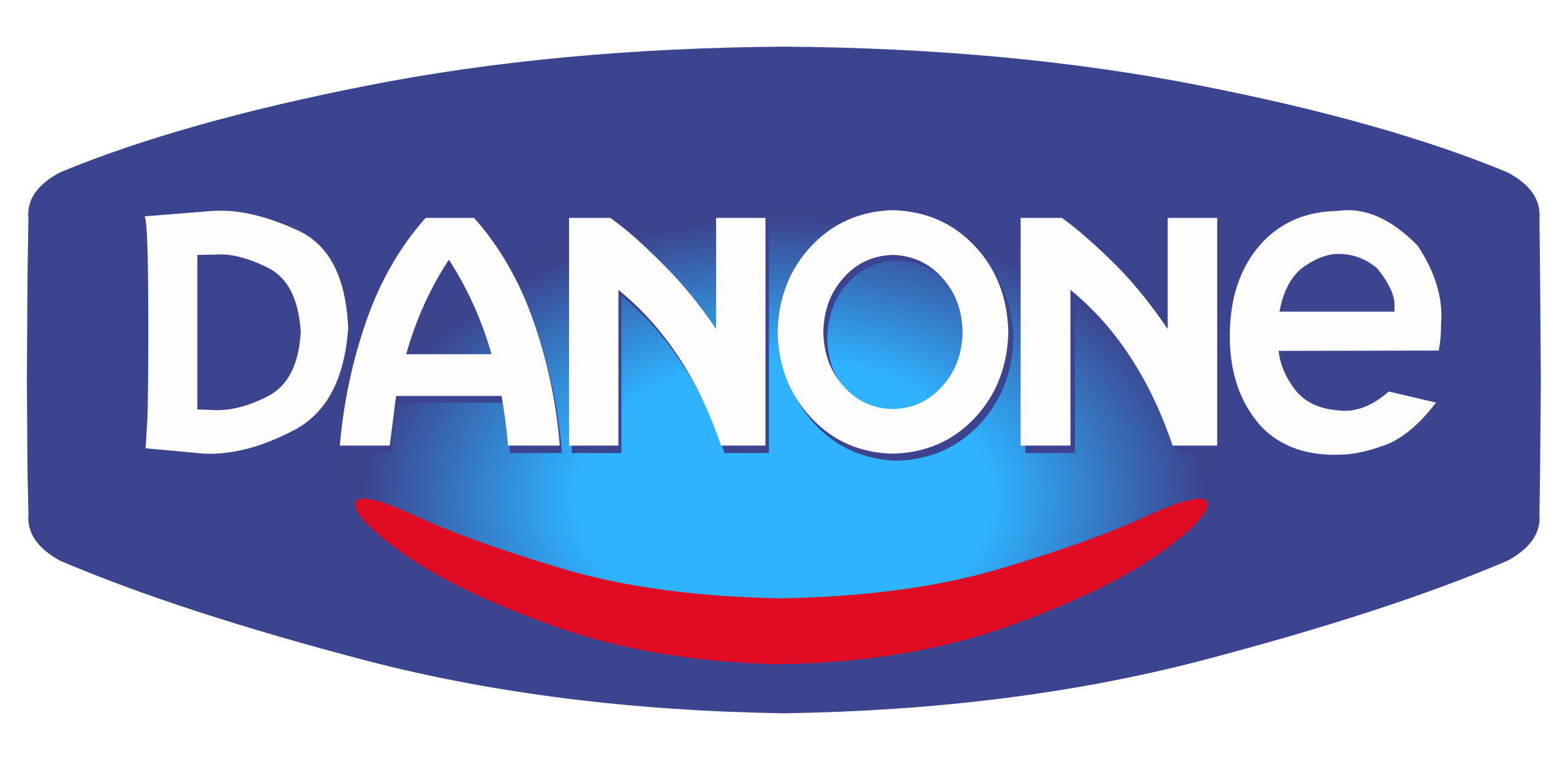
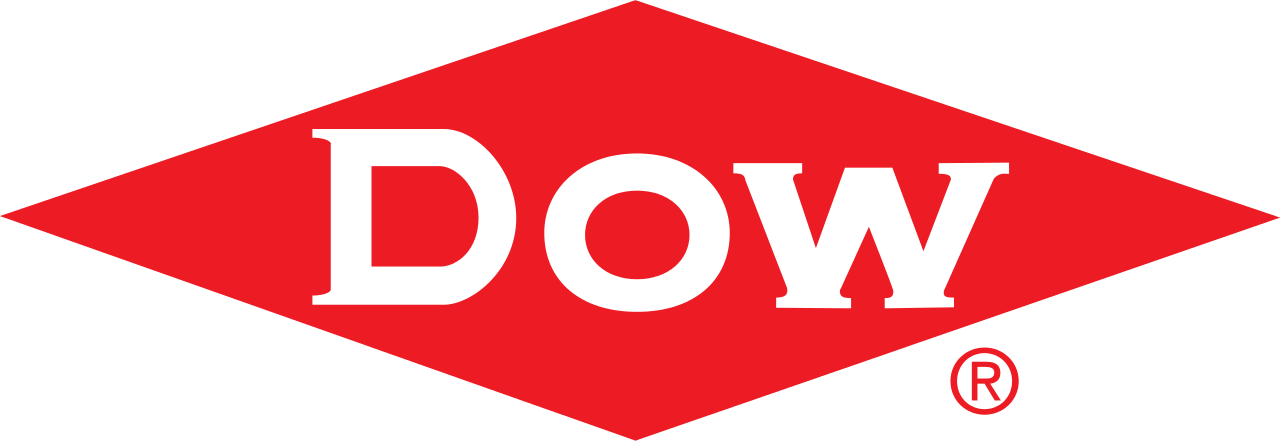
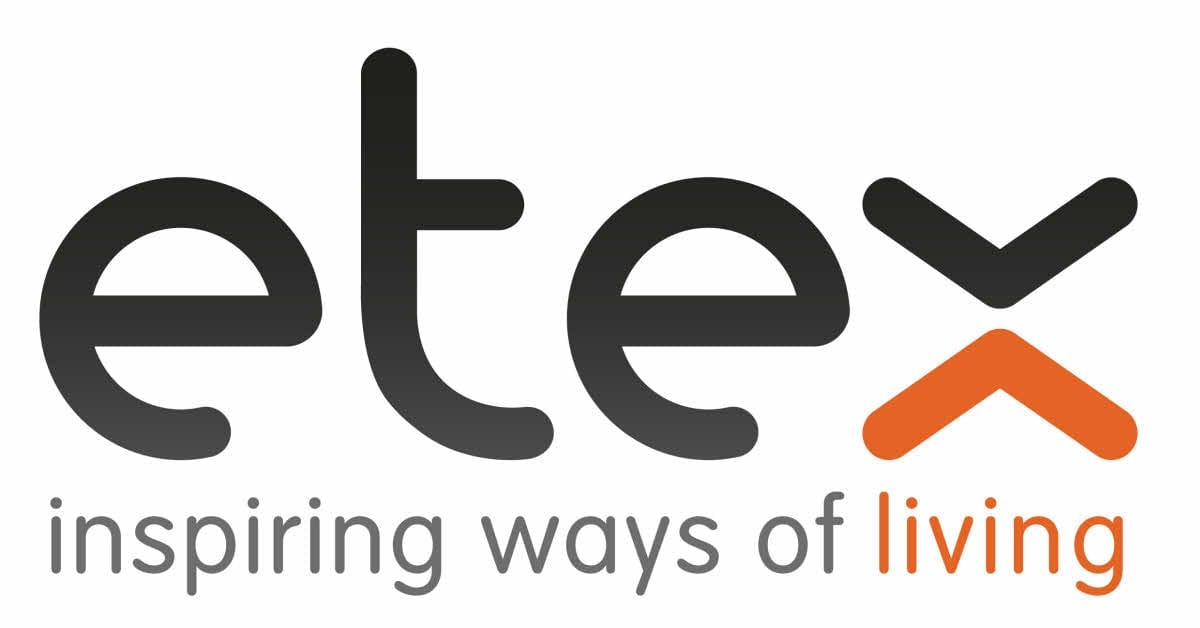
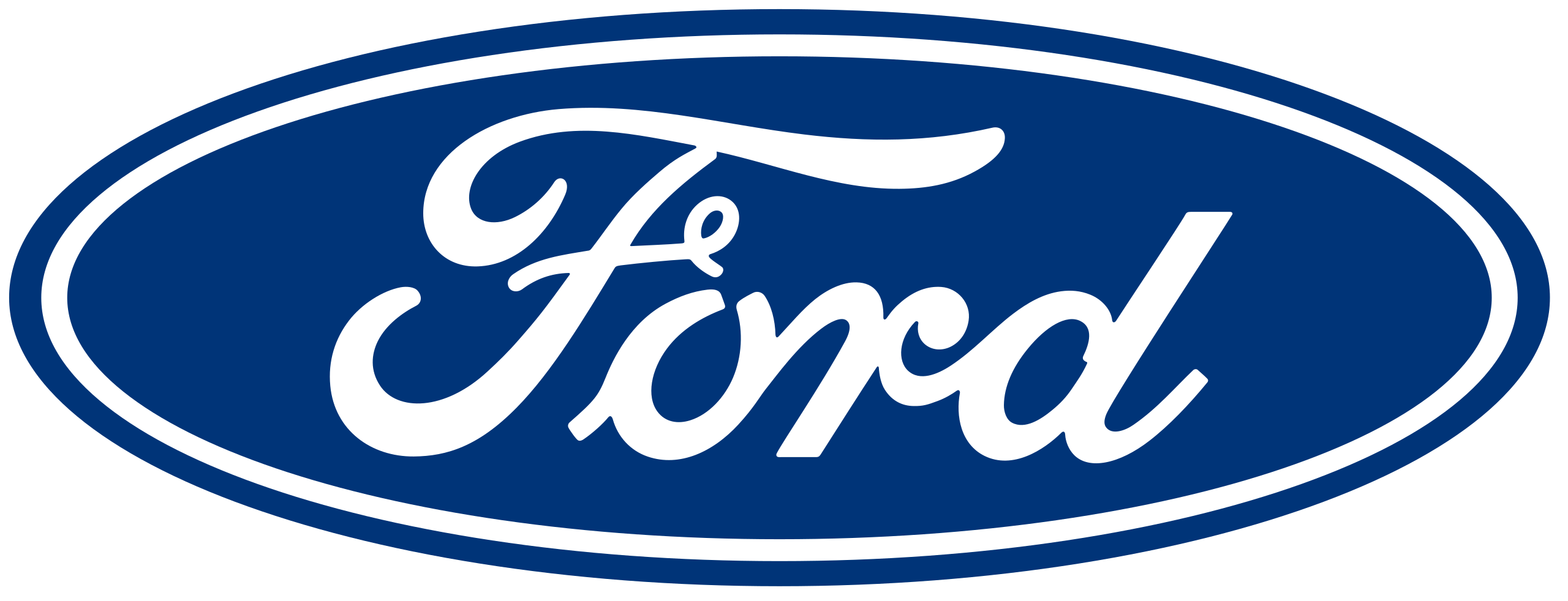
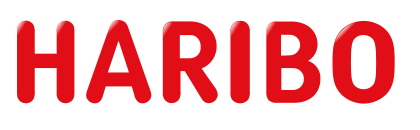
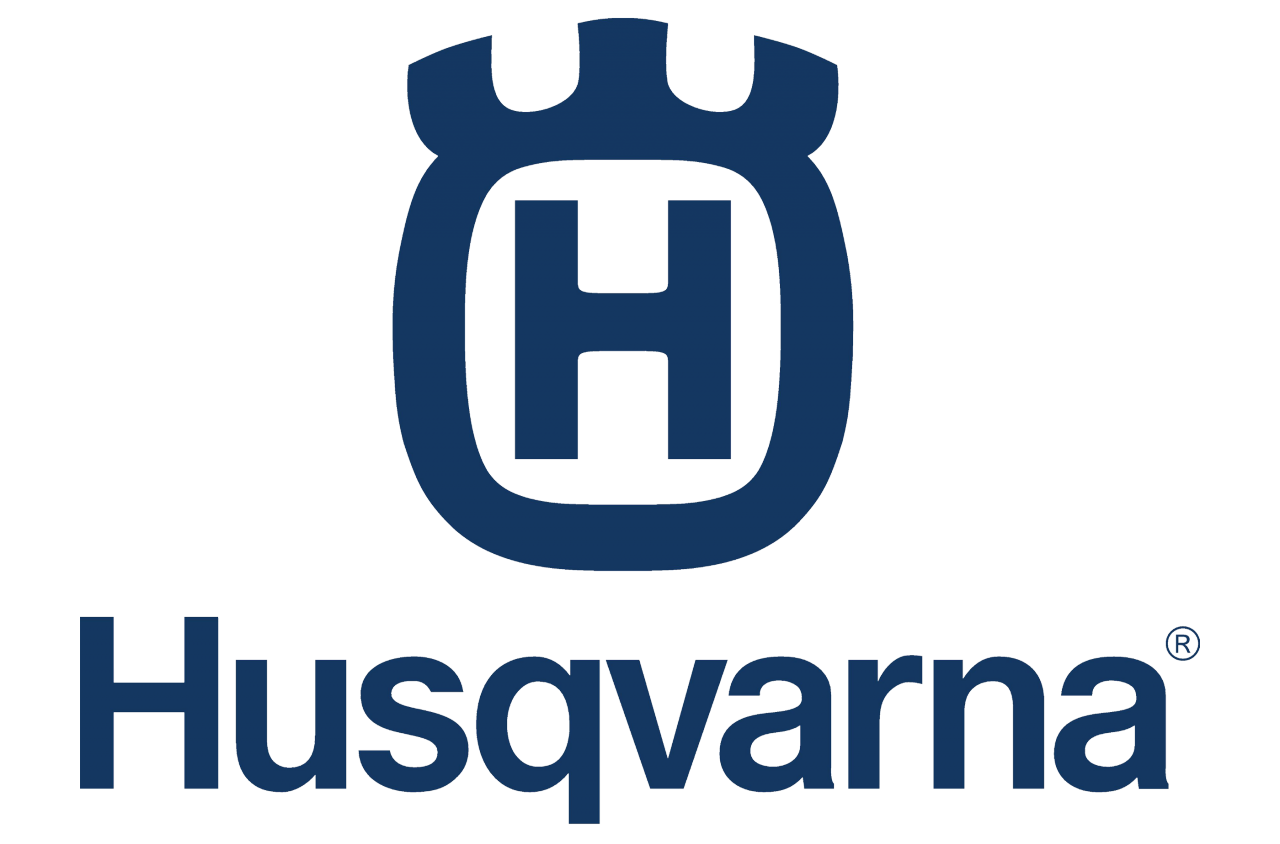

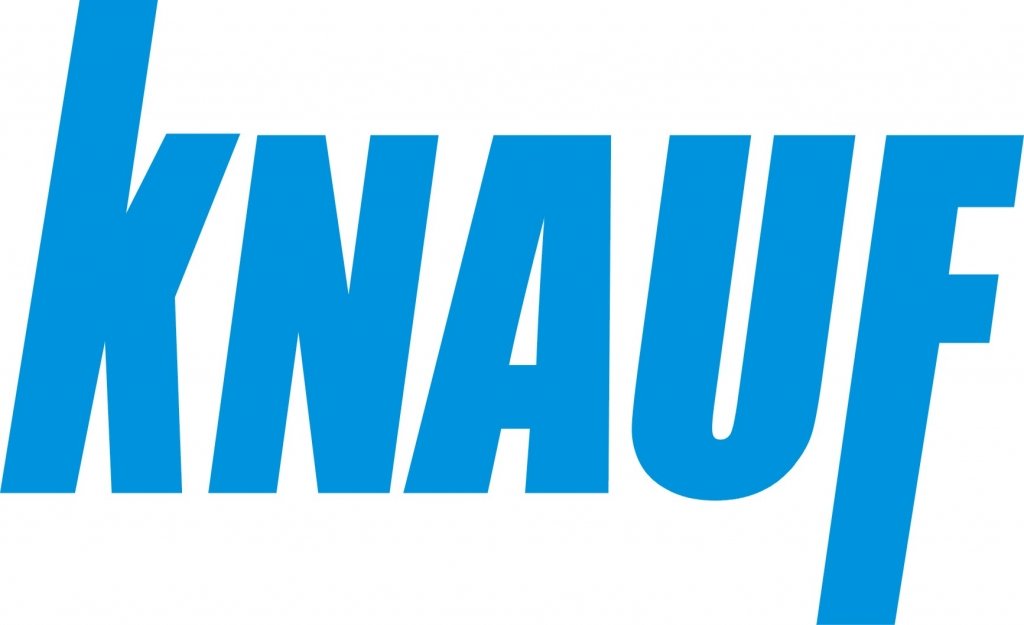
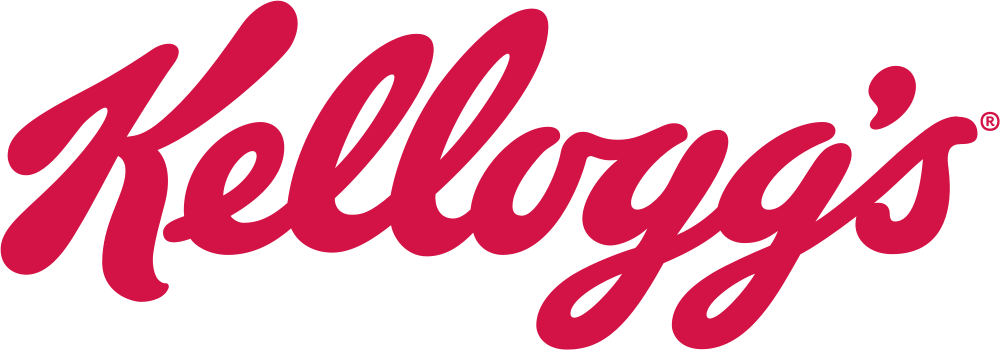
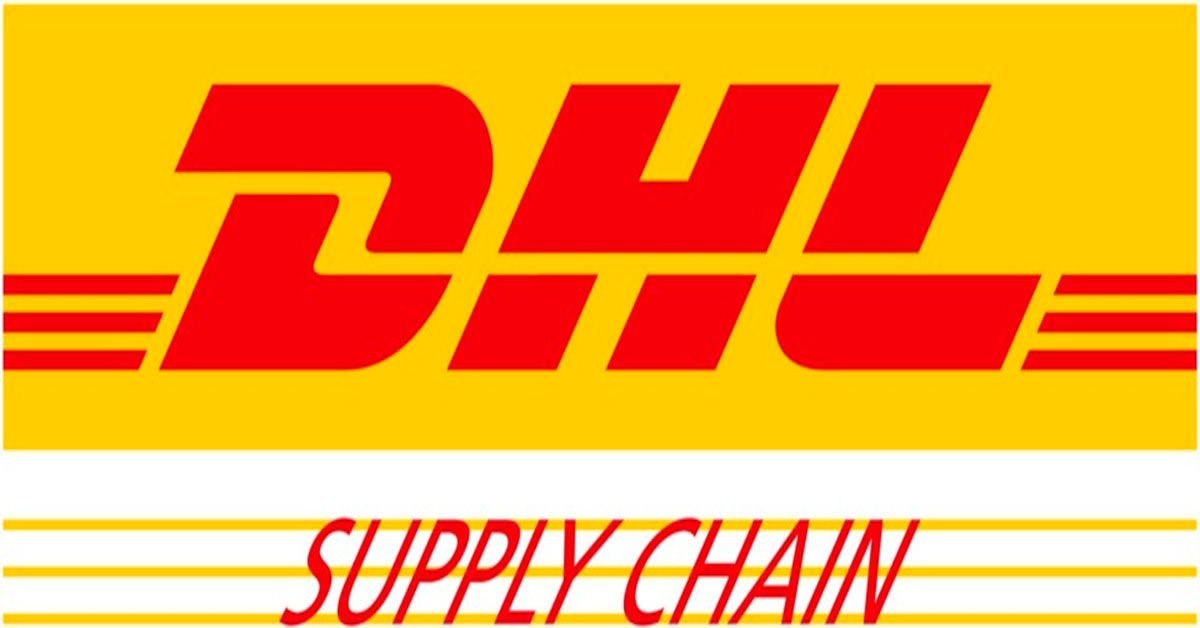
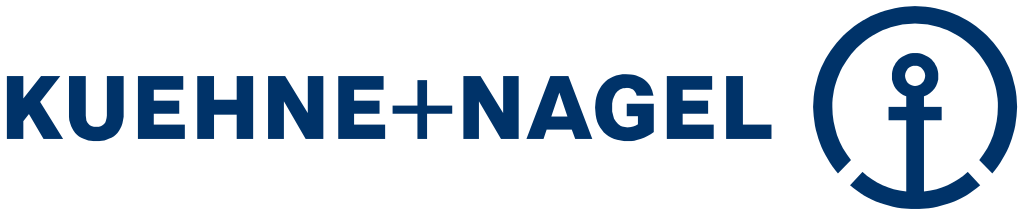
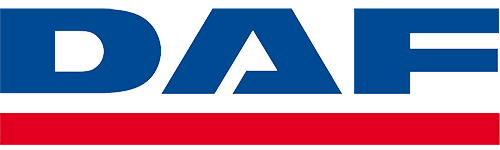
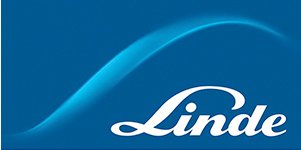
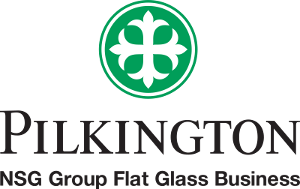
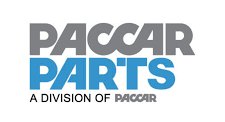
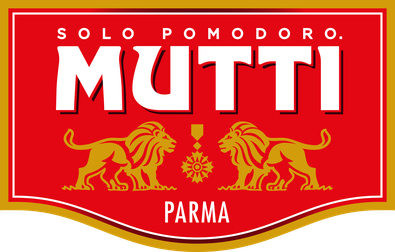
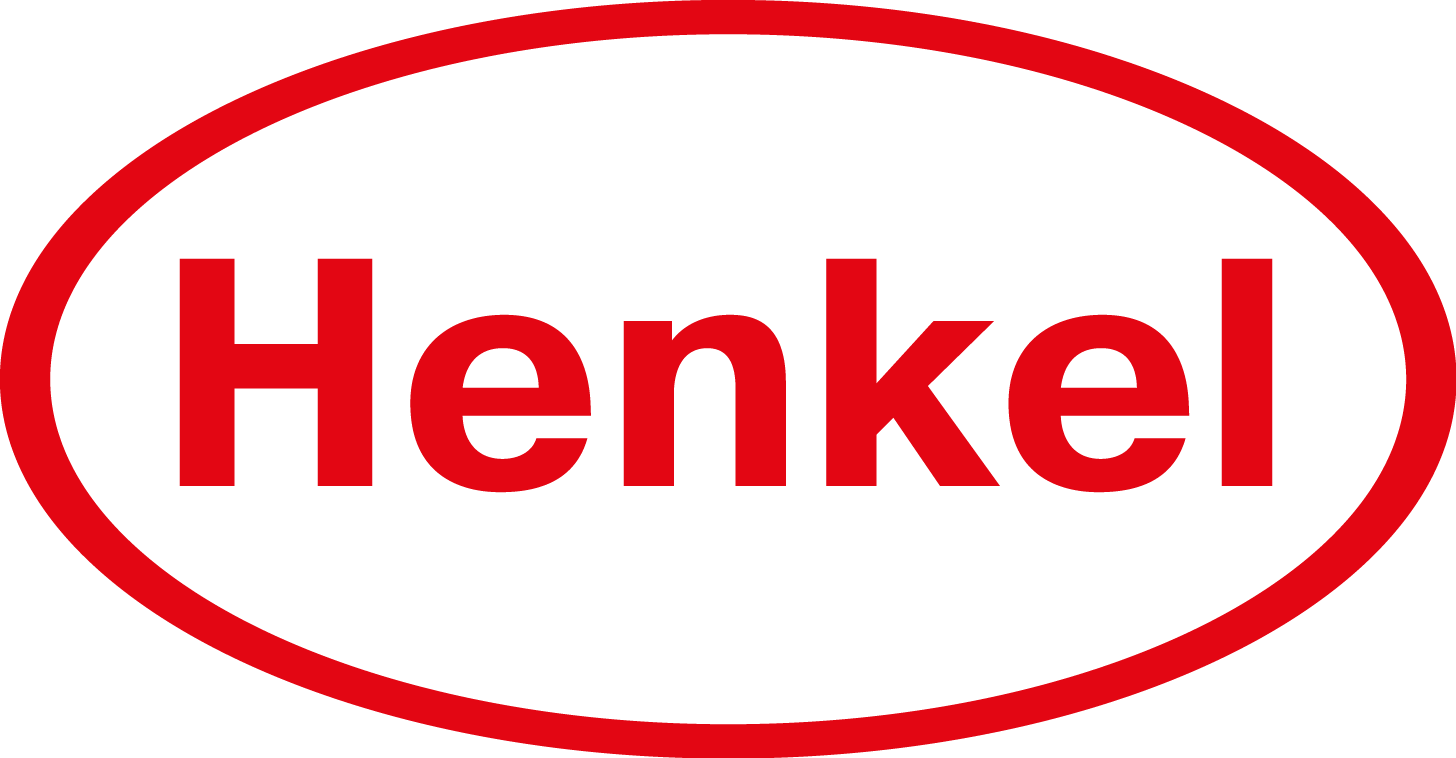
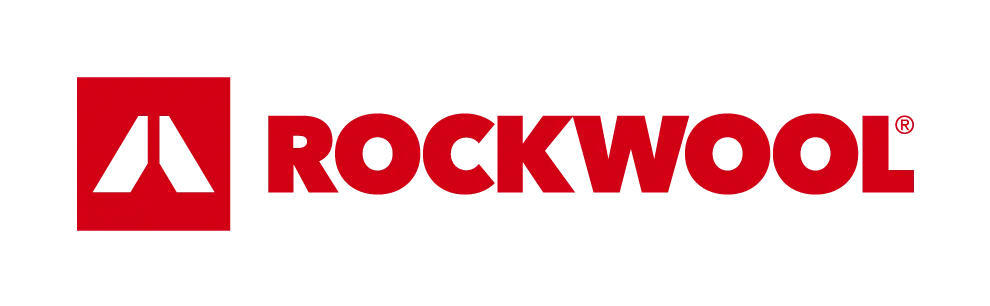

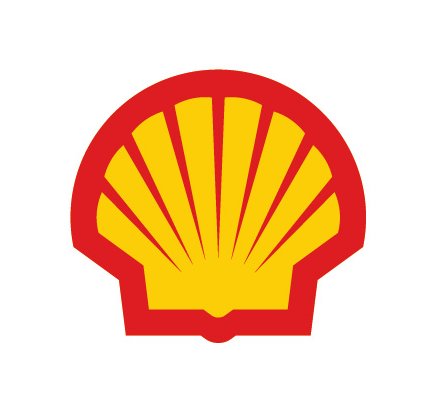
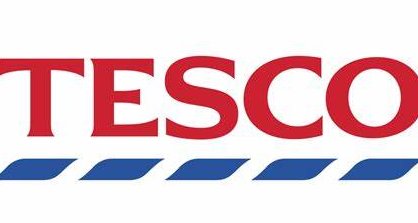
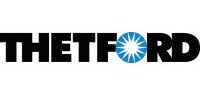
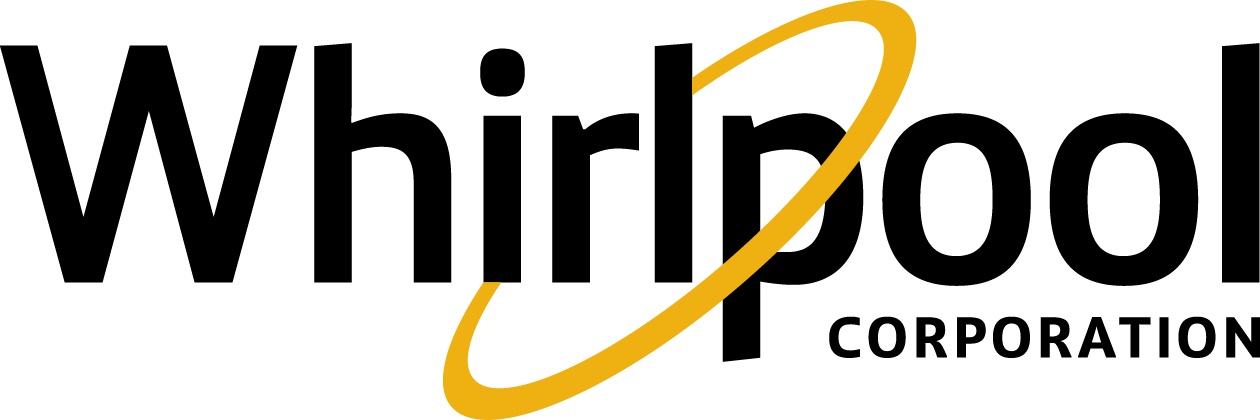
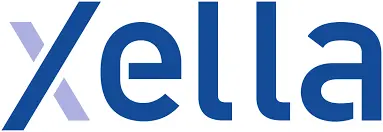
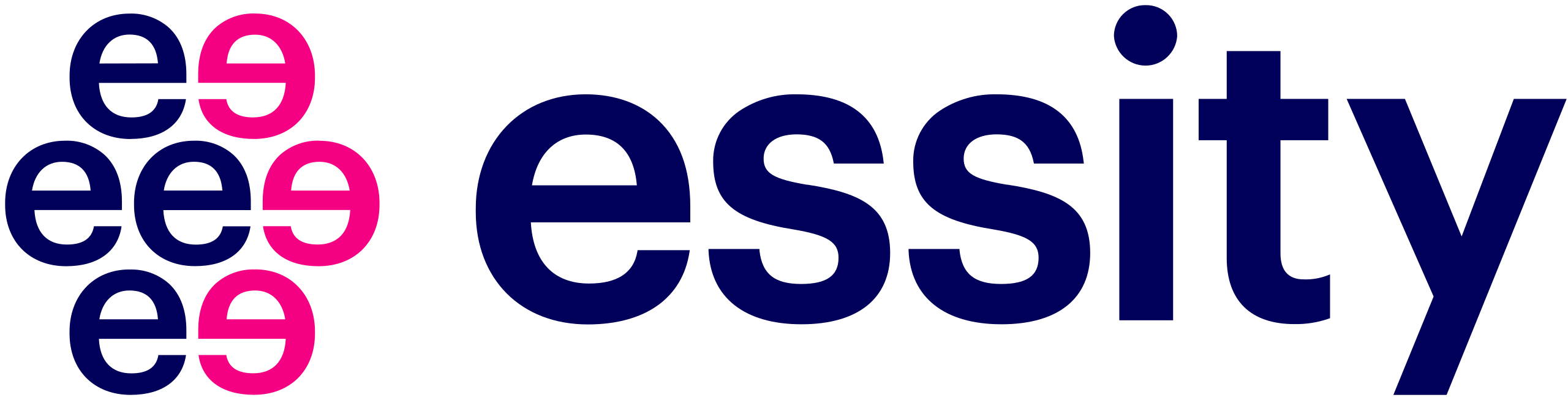
Explore our product solutions
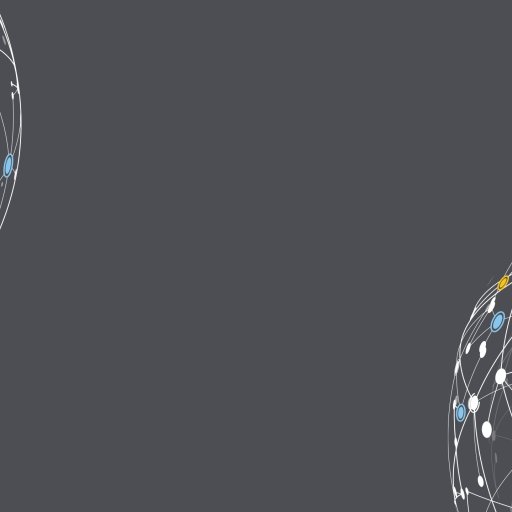
Trimble and Transporeon: Better Together
Transportation connects everything
Trimble acquired Transporeon in April 2023 to further develop and offer solutions that address both the physical and digital realities of commercial transportation. Both Transporeon and Trimble have a deep understanding of the importance of transportation's role in connecting our world. Learn more about how Transporeon and Trimble are shaping the future of global supply chains.
Case Studies
Discover real-life examples of how our clients have transformed their businesses by leveraging Transporeon's Transportation Management System.
Events and webinars
Meet Transporeon’s world-leading experts in person, or join us and our partners online for in-depth information and latest innovations.
Used daily by more than
Publications
Check out our library of reports, white papers and eBooks, featuring market experts' views and insights.