Transporeon makes moving freight as easy as possible.
For more than 20 years, Transporeon has been digitising and transforming logistics. The Transporeon transportation management platform is an essential part of the shipper/carrier ecosystem while linking people, places and things.
We connect, encourage collaboration, enable efficiency and automate ease for transportation operations and supply chain with our autonomous dealmaking, execution & visibility, dock & yard management and tech-driven freight audit solutions.
AI, data-driven analytics, autonomous, automation…these are buzzwords for some, but they are built-in for us. Transporeon’s cloud-based transportation management software enables thousands of customers every day, and powers the largest network of shippers, suppliers, retailers, goods recipients and carriers in the world. And as the newest member of the Trimble family, that network is now even bigger.
Got freight? Get Transporeon.
The company we keep
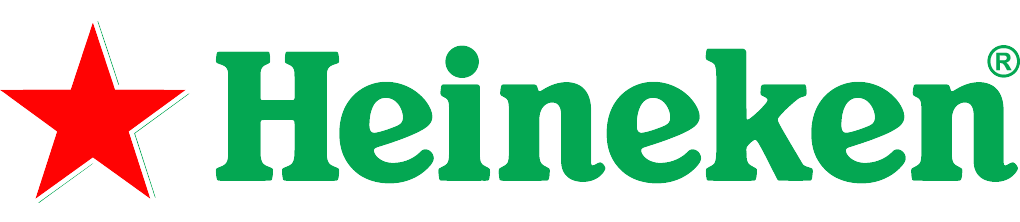
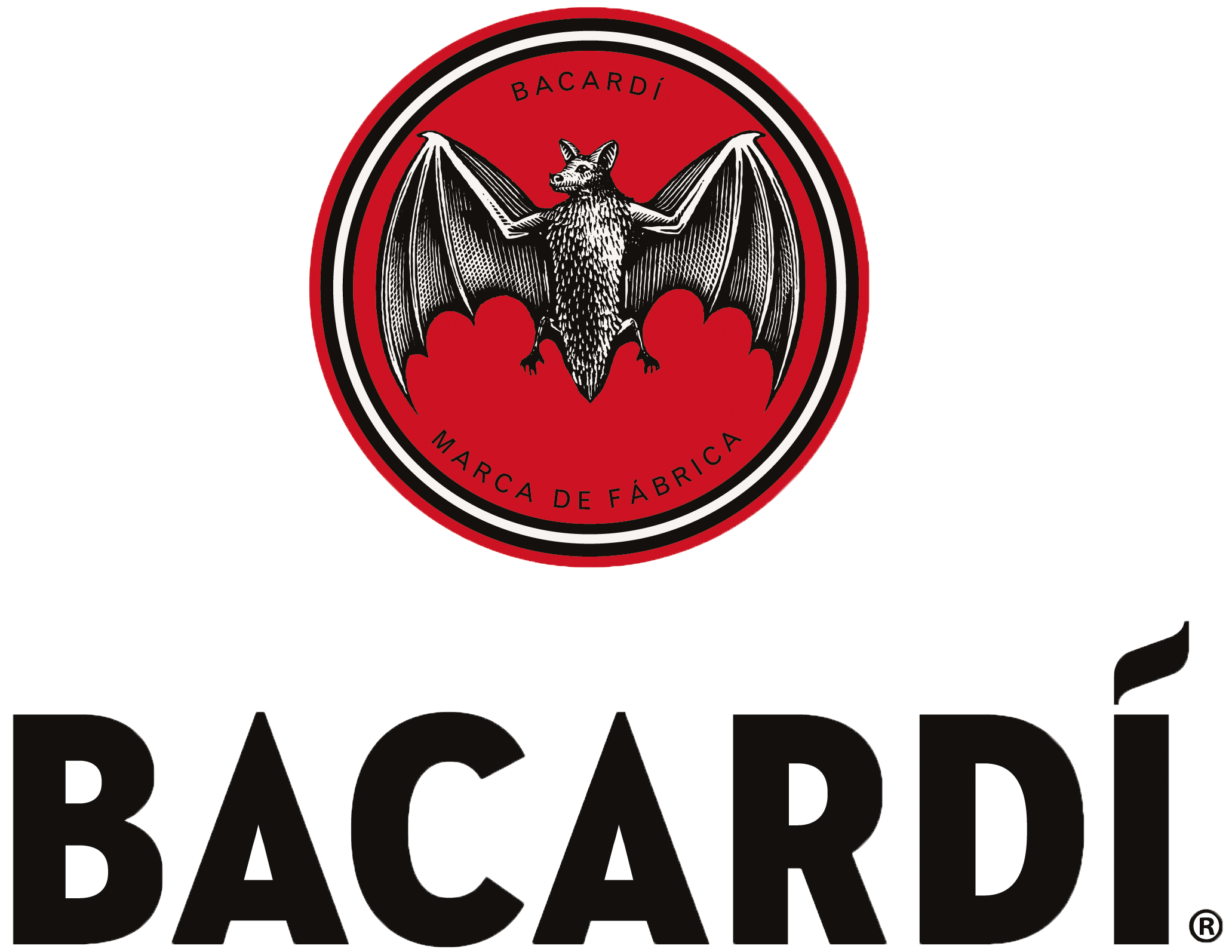
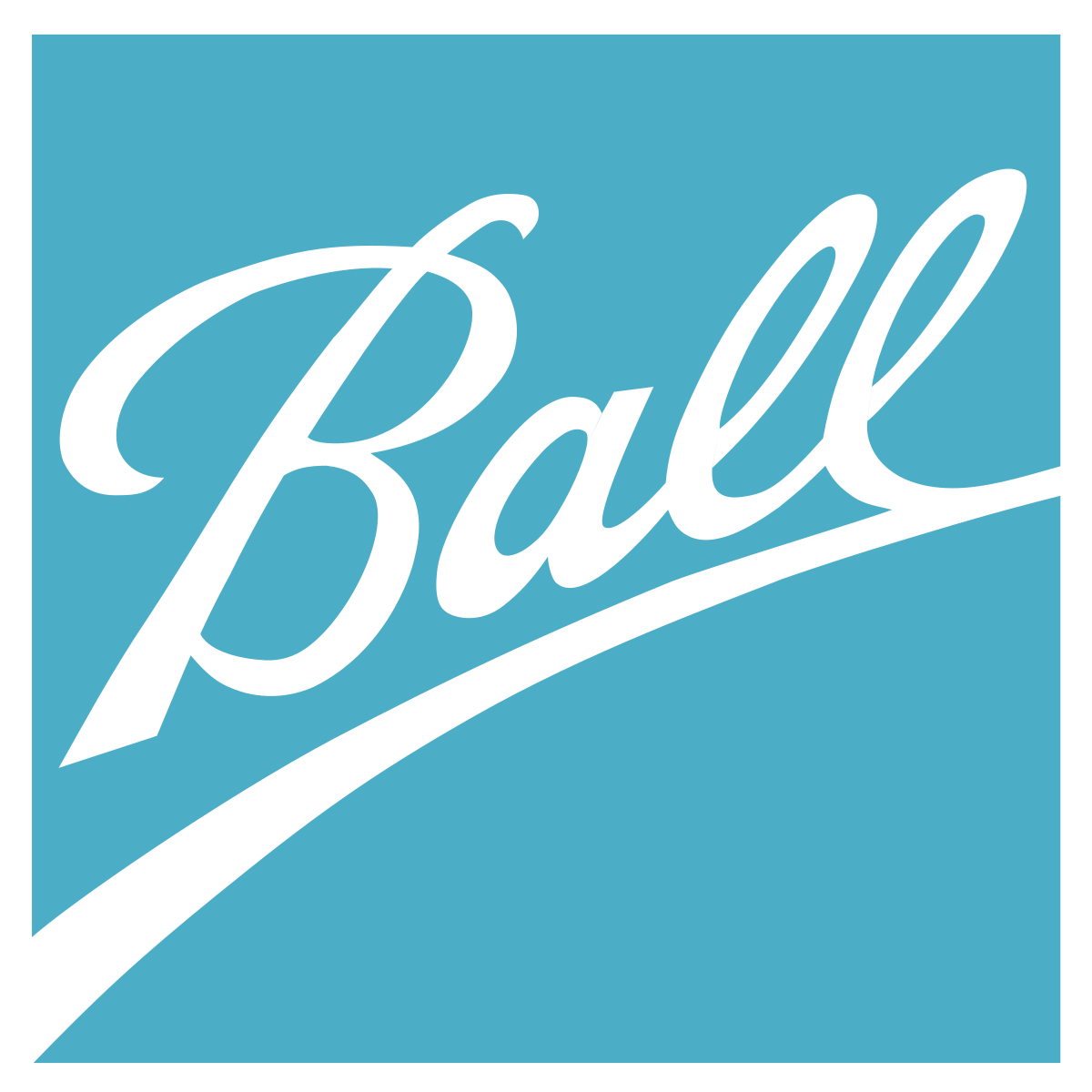
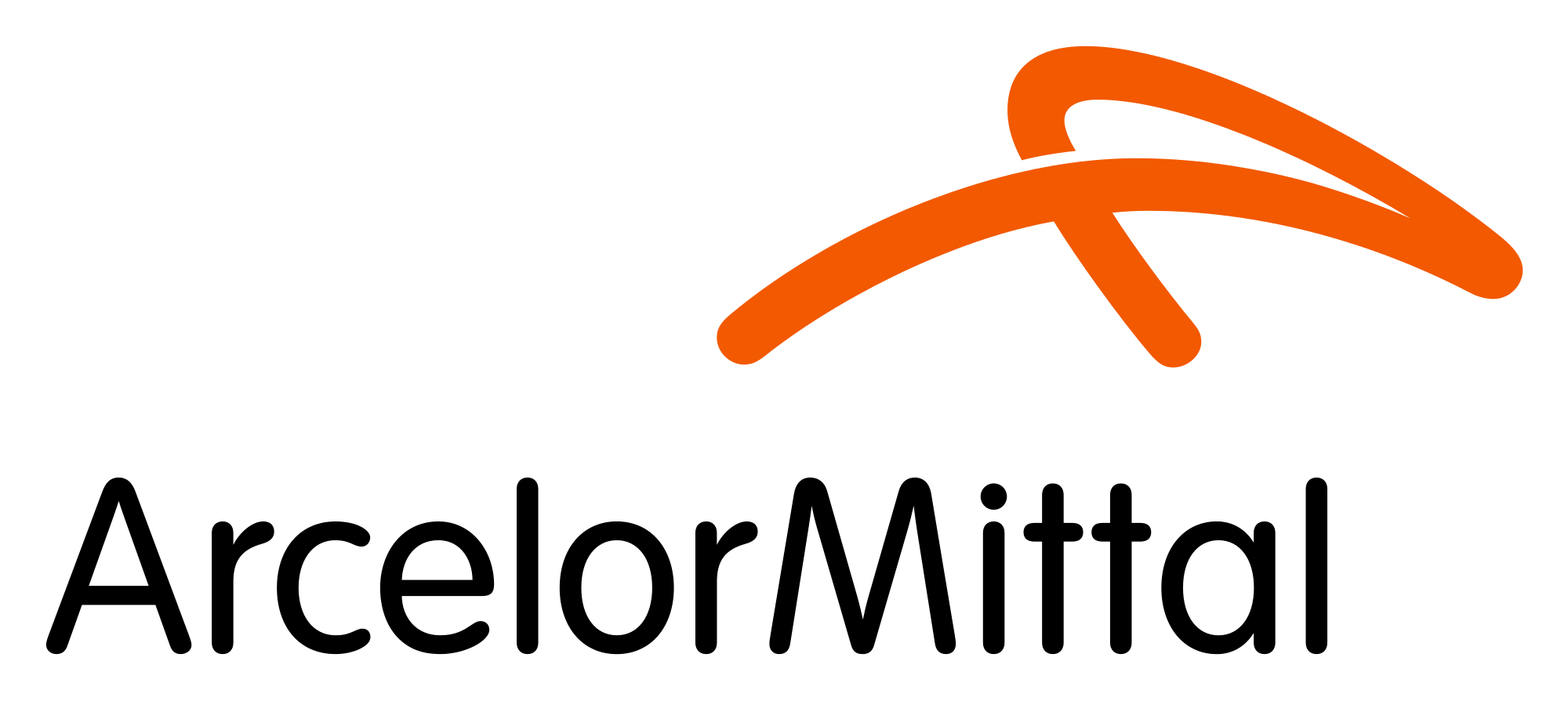
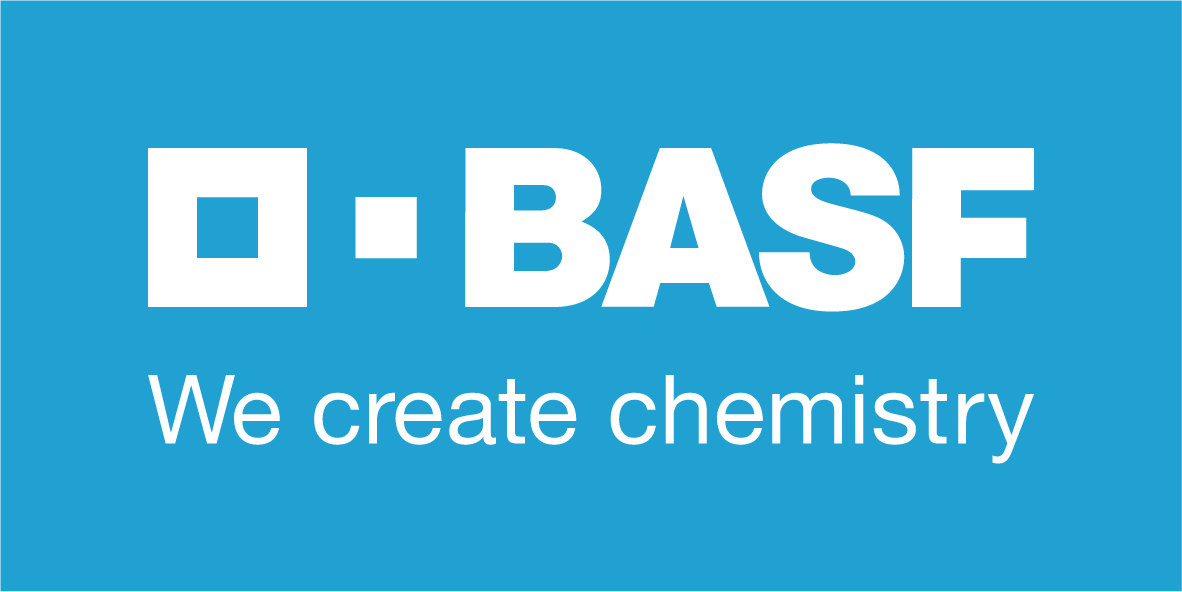
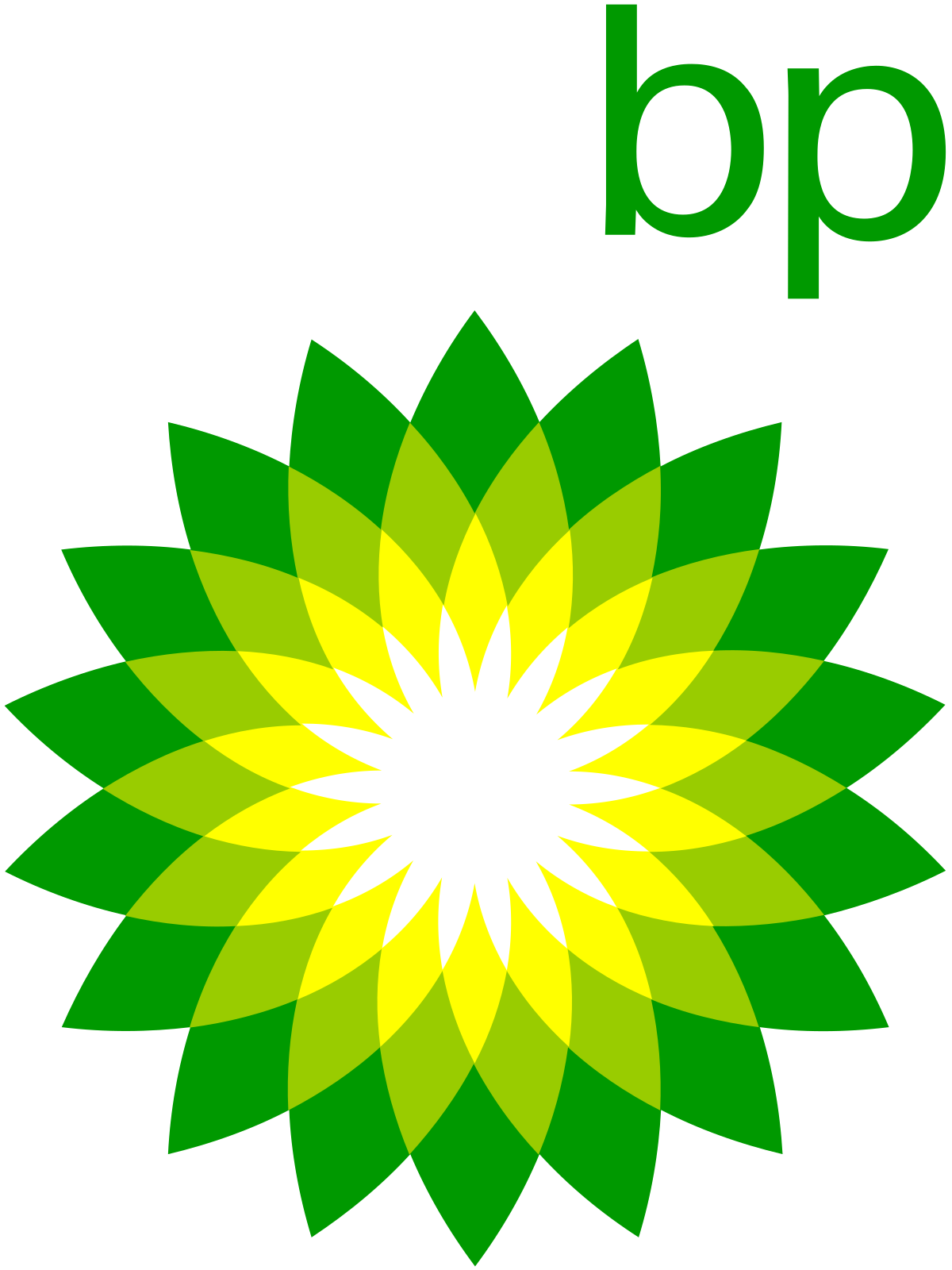
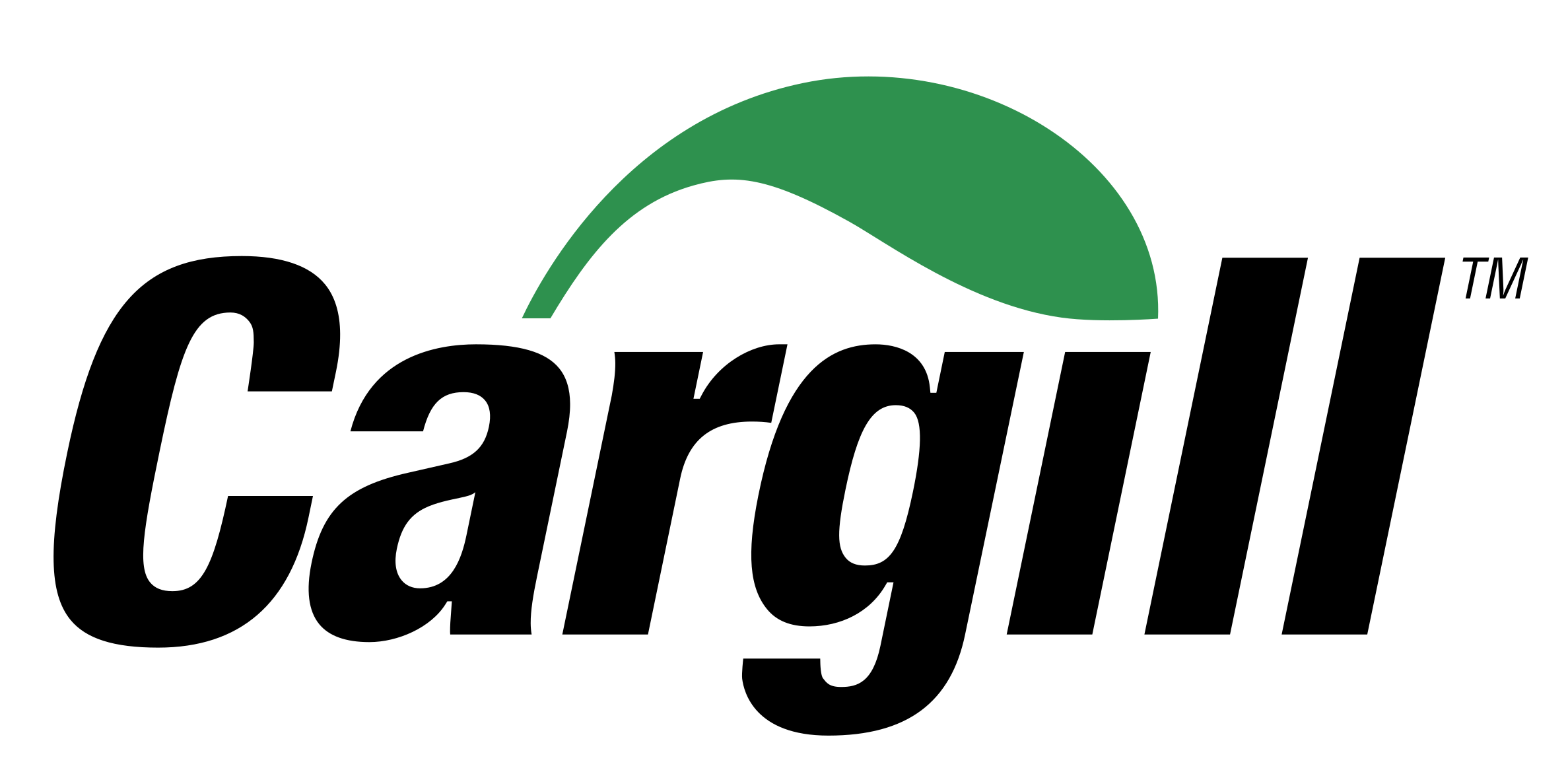
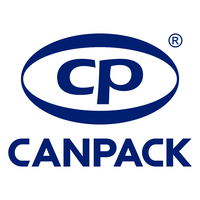
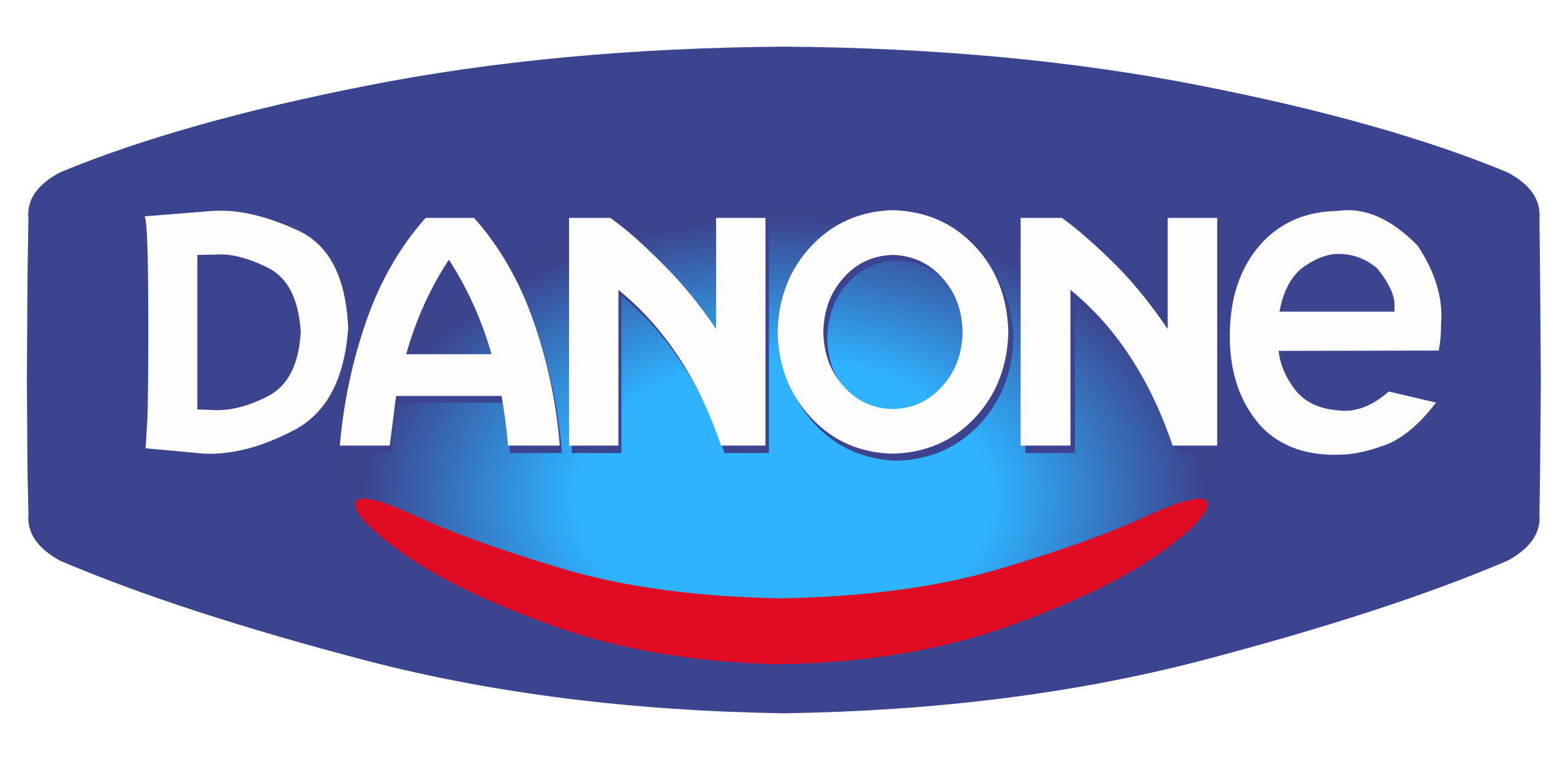
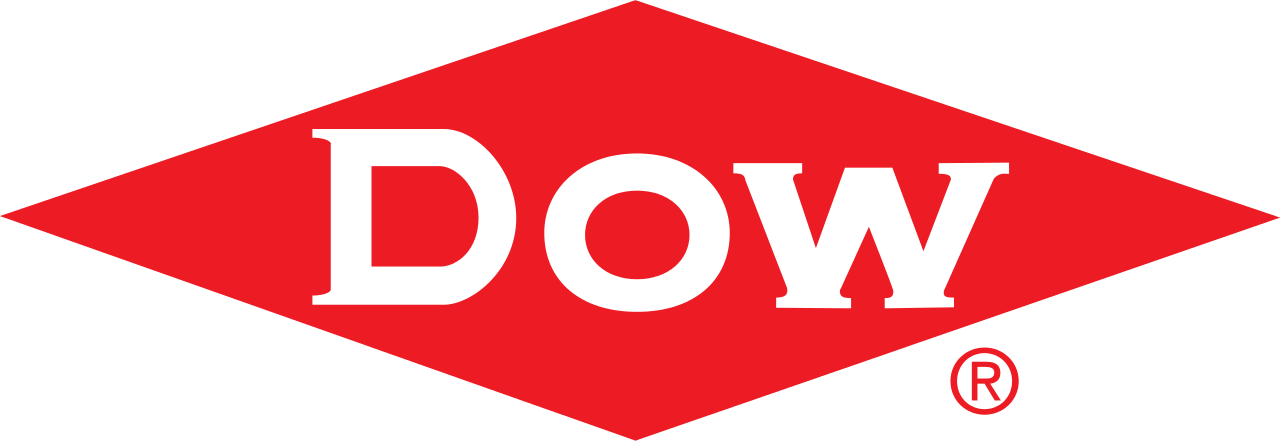
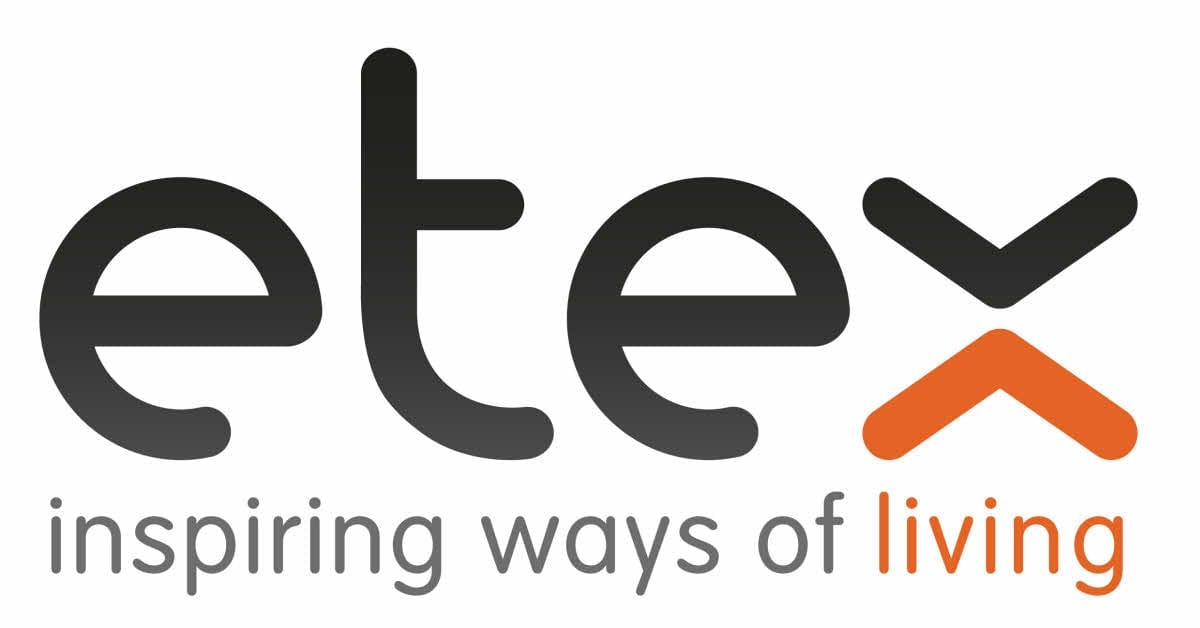
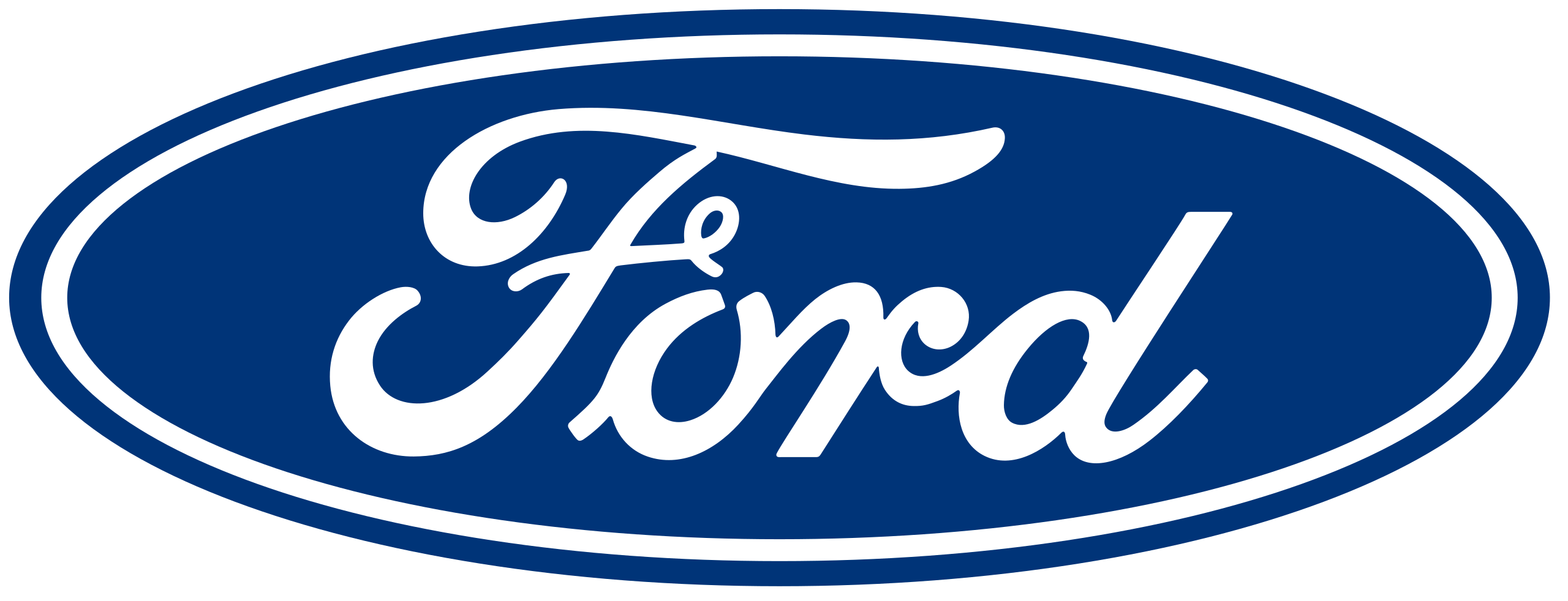
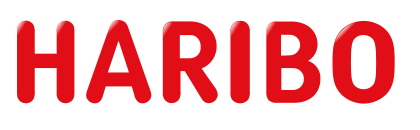
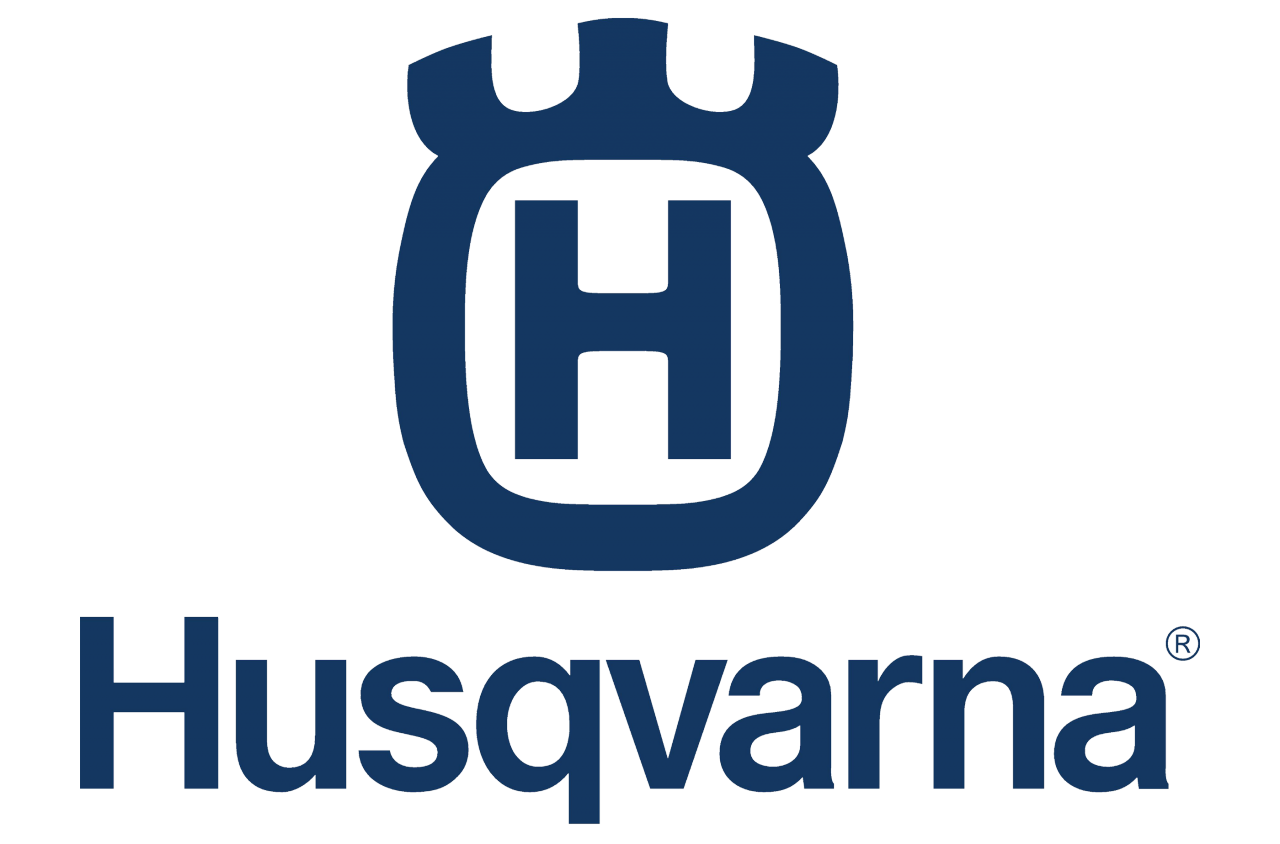

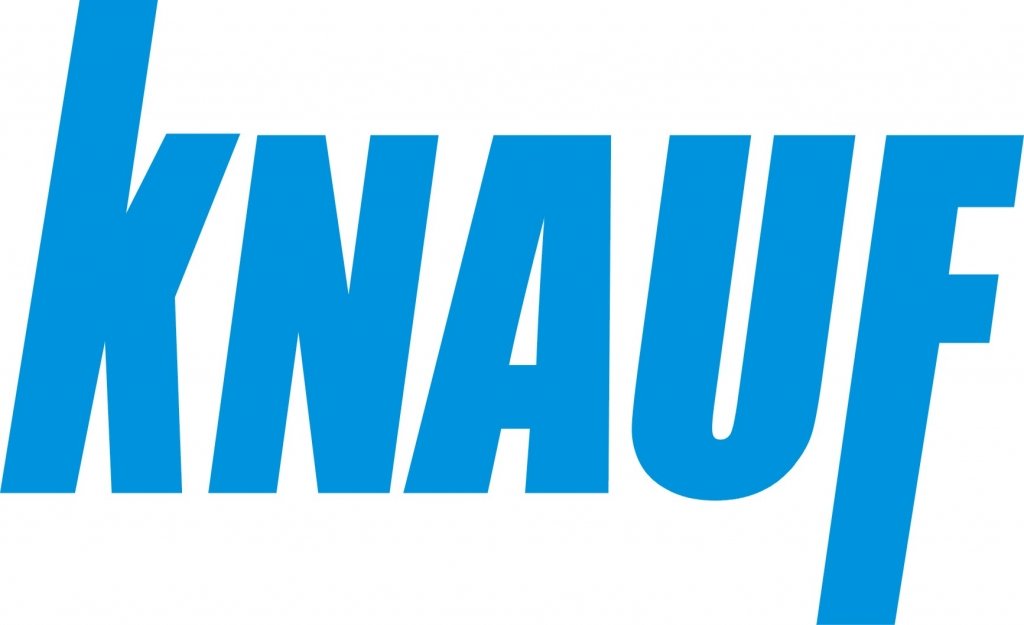
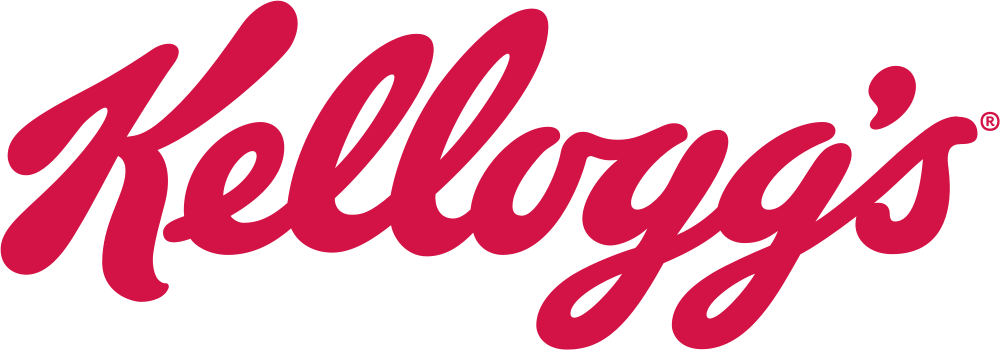
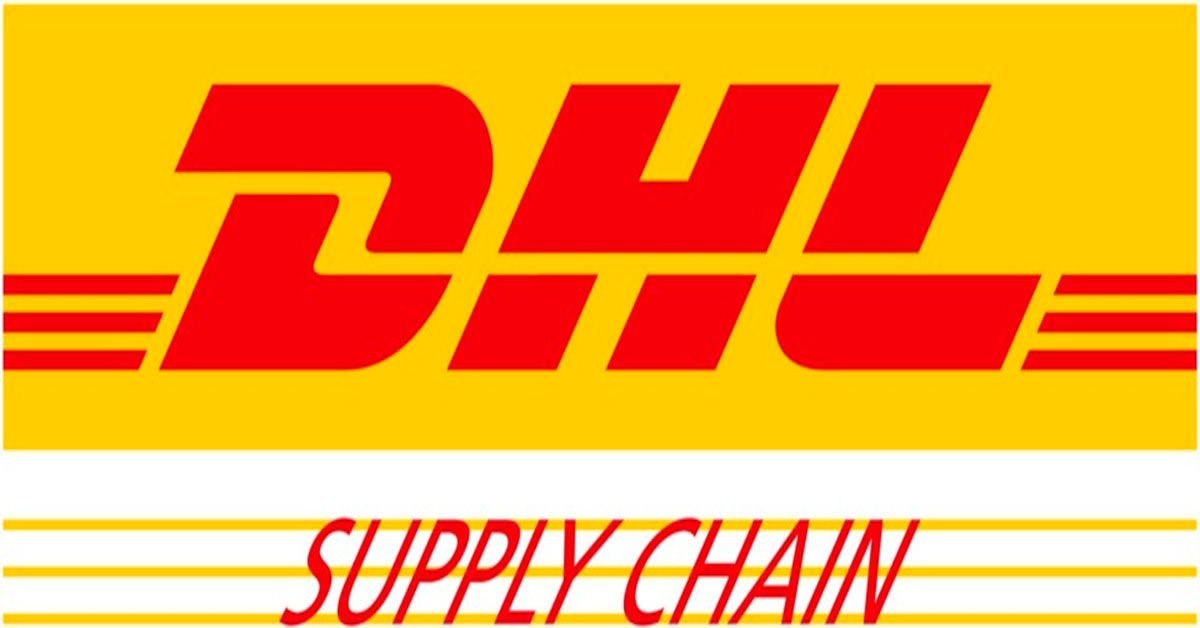
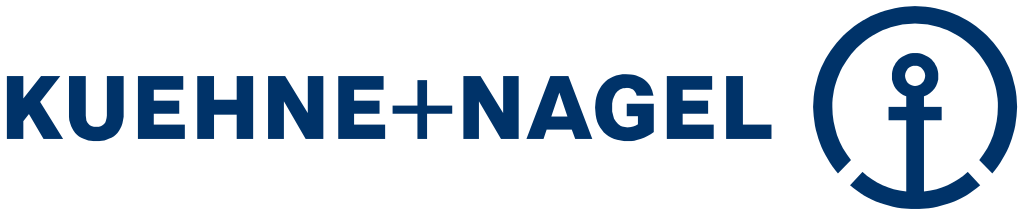
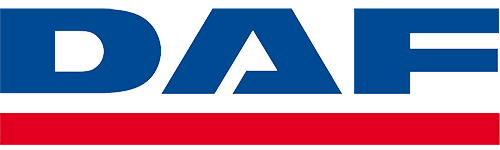
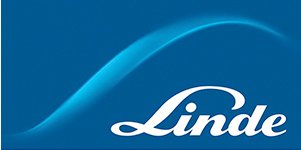
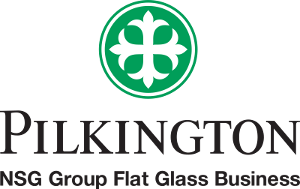
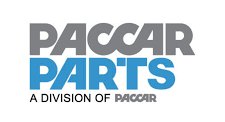
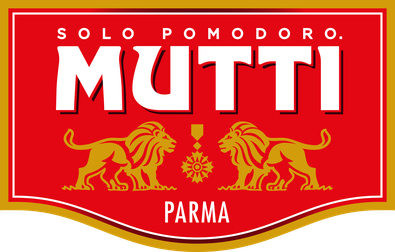
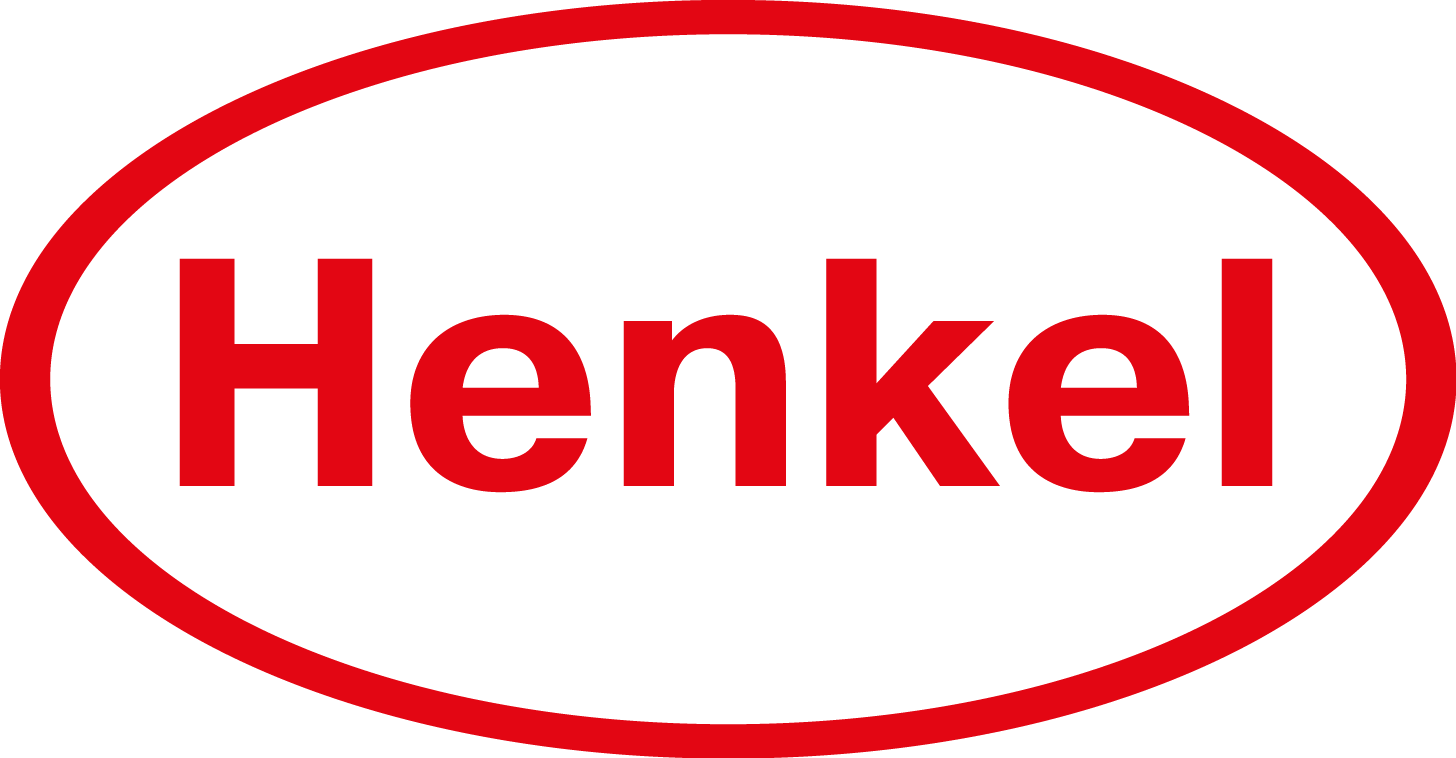
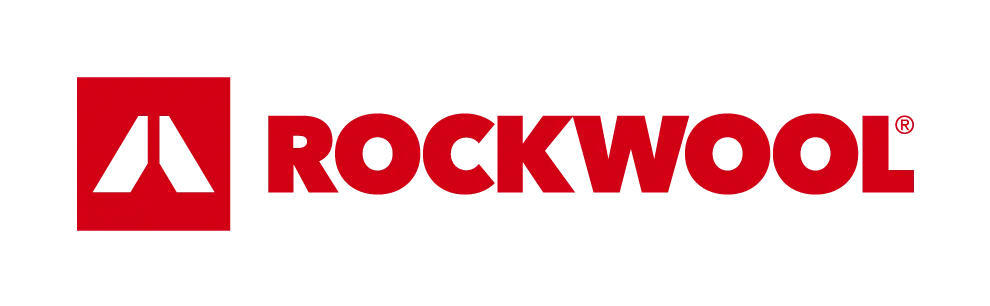

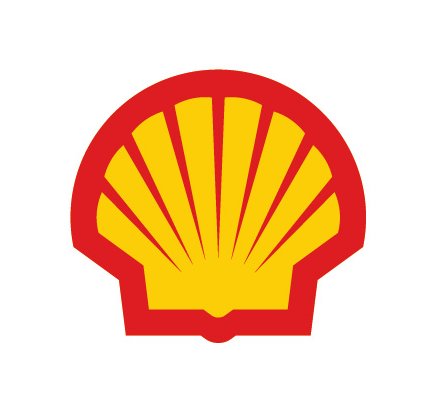
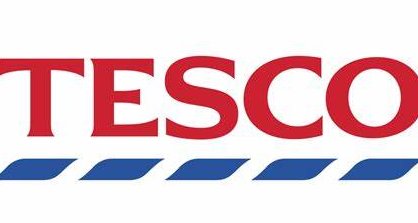
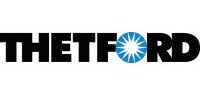
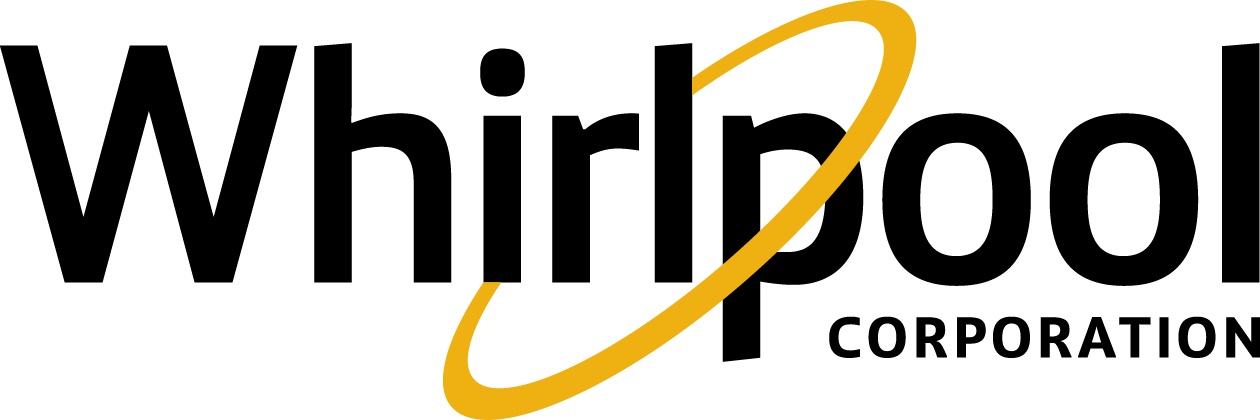
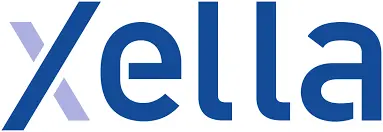
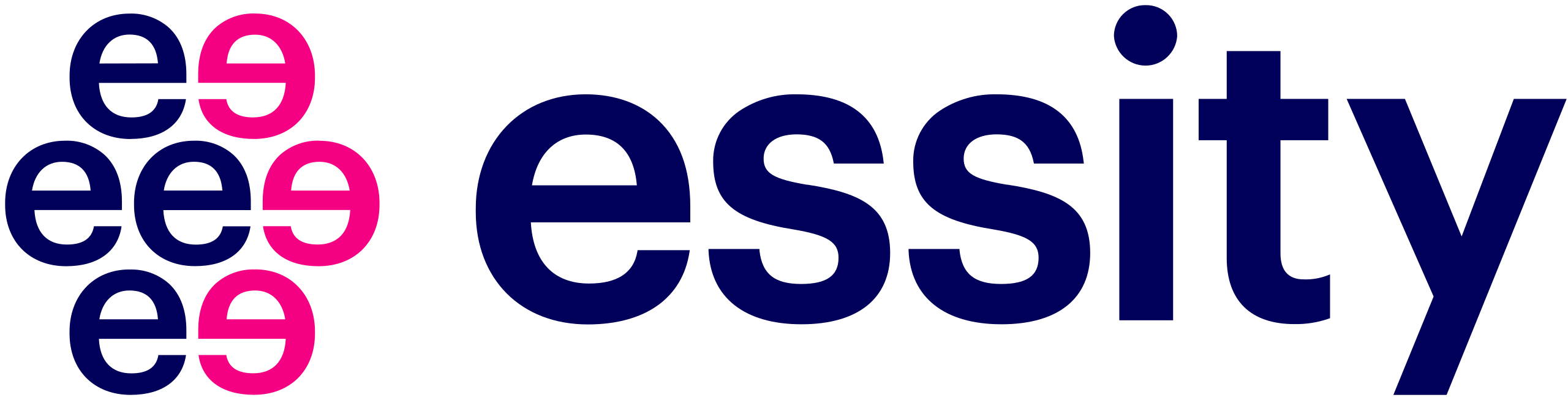
Explore our product solutions
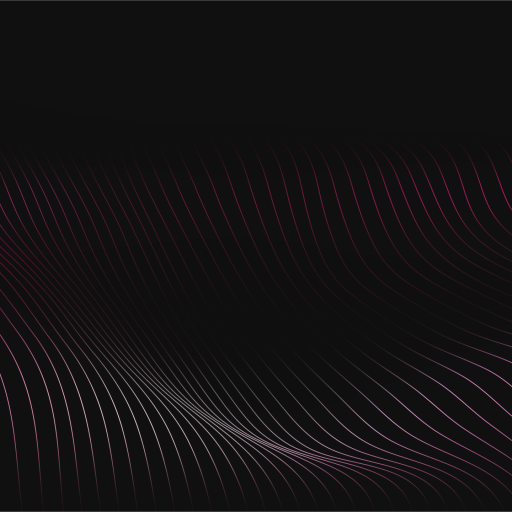
TRANSPOREON’S AI SOLUTIONS
The future of logistics isn't coming soon; it's here.
Harness the power of AI-driven spot freight optimisation with Autonomous Procurement, AI-powered freight quoting with Autonomous Quotation, and market development predictions with Market Insights. Gain predictive ETAs, and experience simple carrier onboarding with our AI Agents. Revolutionise your logistics with intelligent automation and data-driven insights.
Case Studies
Discover real-life examples of how our clients have transformed their businesses by leveraging Transporeon's Transportation Management System.
Events and webinars
Meet Transporeon’s world-leading experts in person, or join us and our partners online for in-depth information and latest innovations.
Big efficiencies, big network
Publications
Check out our library of reports, white papers and eBooks, featuring market experts' views and insights.